Equipment maintenance of presses
Issue
Presses often fail in the piercing process of high tensile steel sheets
- Due to frequent press breakdowns, forming speed has been reduced, but breakdown frequency has remained almost unchanged.
- Production is declining and production plans are often disrupted.
- Press repair costs are increasing, as well as labor costs for troubleshooting.
Solution
Two of the six bolts in the connecting rod section of the press were replaced with PiezoBolt piezoelectric load sensors to monitor load fluctuations during forming.
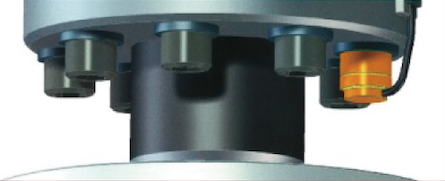
The results showed that breakthrough phenomena occurred under 80 SPM conditions, but were minimized at 120 SPM. The overall load load was also found to be reduced by 37% at 120 SPM, so the production speed was changed to 120 SPM. This reduced the load on the presses, and the frequency of press breakdowns was steadily reduced.
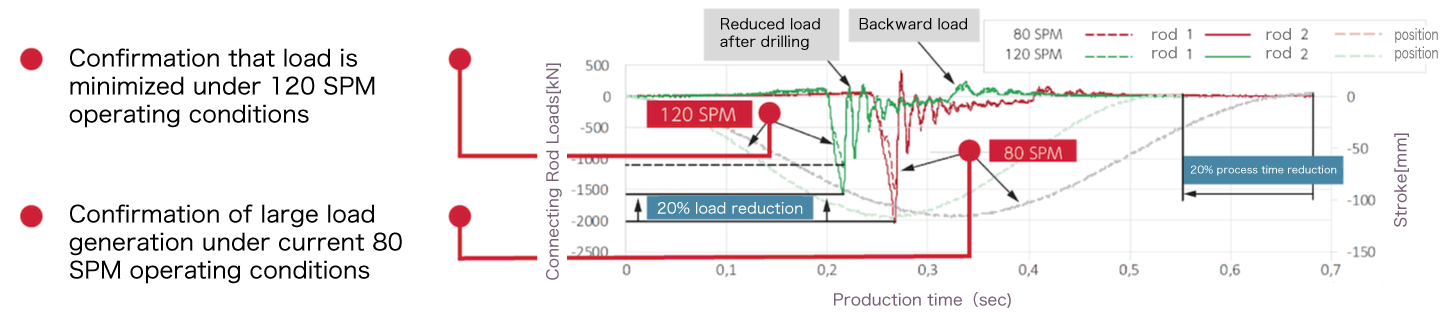
Result
Reduce press machine failure frequency by optimizing forming conditions
- Identified the cause of the malfunction and made it possible to perform forming with as little burden on the equipment as possible.
- Reduced repair and labor costs due to breakdowns.
- The measurement results enable us to consider not only the load condition of the press equipment, but also the causes of product defects.
Customer Testimonials
I was attracted by the fact that the state of the press equipment can be checked at any time by monitoring changes in load for each shot in press forming in real time. Since it is a bolt type, it can be fastened to any part of the press equipment, and I thought it could be utilized for various issues in the future.
Industry: Automobile parts manufacturer
Products Used:
- Piezoelectric Load Sensors PiezoBolt
- DeveloperSenses
- Wire type linear sensor
Case Study List
- Detecting tool crack propagation
- Die breakage detection
- Life prediction by punch abrasion
- Lubricant Evaluation
- Detecting punch breakage
- Foreign object strike detection
- Detecting adhesion of scrap
- Visualization of press forming
- Equipment maintenance of presses
- Failure detection of cutting tools
- Detecting anomaly of die casting