Failure detection of cutting tools
Issue
Unable to determine when cutting tools are damaged
- During processing, the operator is almost always present to listen to the sound and monitor the process, but many defects occur.
- The timing of tool change differs depending on the worker being monitored.
- Tried AE sensor, but it is difficult to predict abnormalities or identify when they occur.
Solution
The bolt that holds the workpiece in place was replaced with a piezoelectric load sensor, PiezoBolt, to measure vibration behavior during cutting.
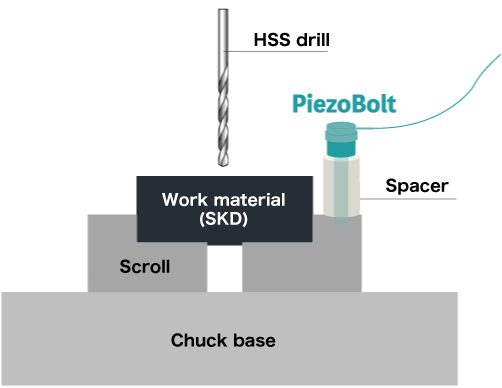
As a result, we were able to detect data changes and predictive signs of cutting tool breakage, abrasion, loosening, and other defects.
By setting the data before and after a cutting tool failure to a threshold value and sending a stop signal, the machine can be automatically stopped just before the failure occurs.
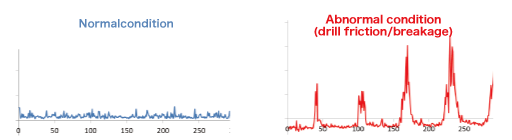
Result
Visualization of cutting tool defects to optimize tool replacement timing
- Machining could be performed until just before tool breakage, and the tool could be used until just before tool life.
- By comparing the measured data, it was possible to review the cutting conditions.
- AI enabled equipment monitoring, allowing the site to be managed with a minimum number of personnel.
Customer Testimonials
The bolt-type design made it easy to install the load sensor near the processing point, which was appealing.
We decided to introduce this system because we thought it could be applied to a variety of tools because of its ability to handle smaller size bolts.
Case Study List
- Detecting tool crack propagation
- Die breakage detection
- Life prediction by punch abrasion
- Lubricant Evaluation
- Detecting punch breakage
- Foreign object strike detection
- Detecting adhesion of scrap
- Visualization of press forming
- Equipment maintenance of presses
- Failure detection of cutting tools
- Detecting anomaly of die casting