Do you have any of these "problems"?
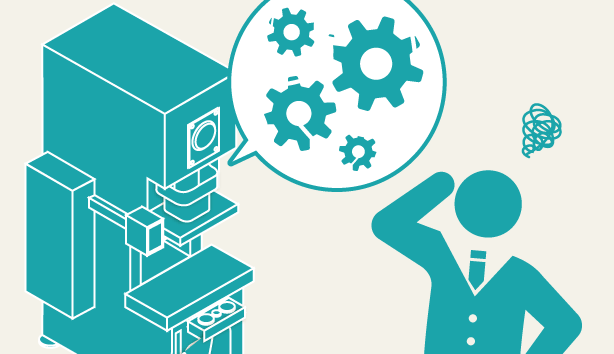
Failure to recognize abnormalities during production results in
a large number of defective products...
Failure to recognize abnormalities in equipment and products at the production site results in large quantities of defective products.
It is difficult to keep personnel to monitor the equipment at all times.
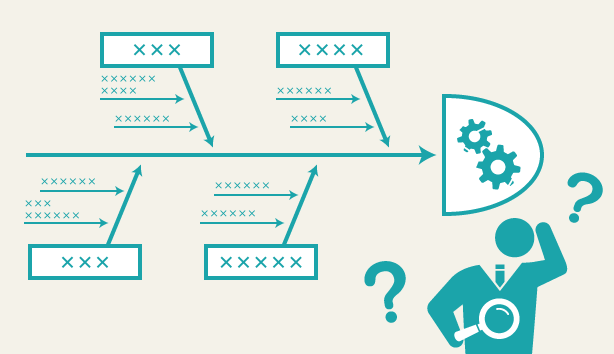
The cause of the defect cannot be identified and
the defect recurrence....
I want to identify the cause of defective products, but I don't know what to do.
We want to determine the cause of the defects and ensure stable production.
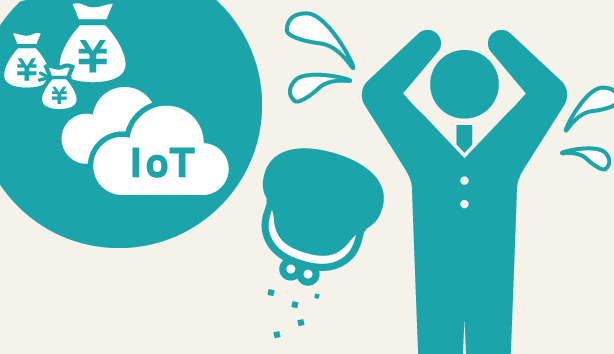
We want to promote IoT in our factories,but
we don't have a large budget...
We want to promote IoT in our factories, but we cannot spend a huge amount of money on replacing or renovating the equipment itself.
Looking for IoT products that can be easily introduced.
Monitoring solutions
can detect abnormalities, maintain equipment and prevent defective products!
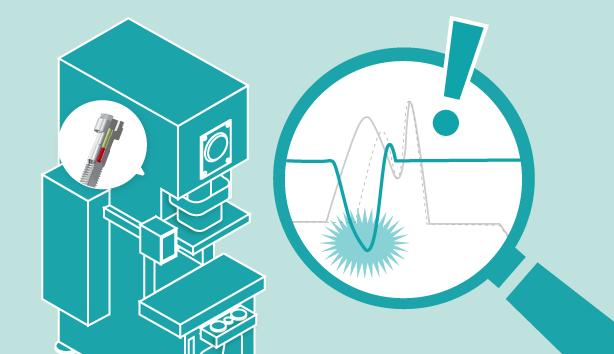
Real-time visualization of signs of abnormality
Installation of IoT sensor which measures loads on equipment and products, enables real-time load measurement.
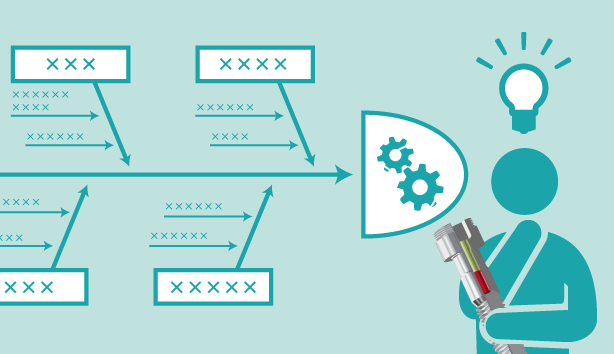
Visualization of processing points and identify the cause of defects
By measuring the load, it is possible to analyze in detail the phenomena occurring at "processing points" that have not been visible until now, and to identify signs of defective products.
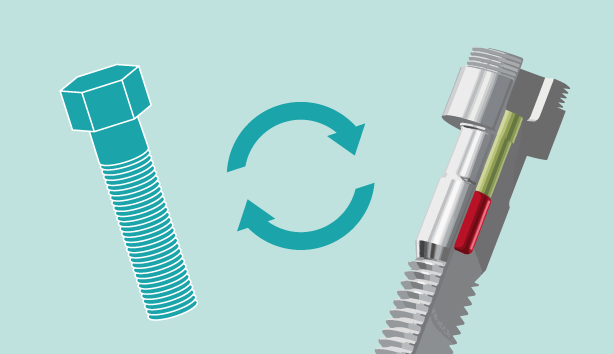
Just Replace the Bolt Easy IoT Installation
Simply replace existing bolts with bolt-type load sensors! You can promote IoT without spending a huge amount of money on equipment replacement or renovation.
What is a monitoring solution?
"PiezoBolt" piezoelectric load sensor is used to measure the load,
this is a solution to "visualize the processing point" that has not been visible until now.
Examples of Abnormality Detection, Defective Countermeasures and Equipment Maintenance
Case Study #1
Detects abnormalities in die cracking and optimizes die replacement timing!
Problem
- Cracks in the die forming section are transferred to the product, resulting in defective products.
- Periodic replacement of dies with short life span settings, which is costly.
Countermeasure
- PiezoBolt is attached to the ring fixture of the die to monitor load fluctuations
Result
- It was found that the degree of progress until transfer to the product can be patterned by the number of occurrences of abnormal waveforms.
- Established a system that counts the number of abnormal waveforms that occur during production and sends out an alarm and stops the equipment when the set number is exceeded.
Reduction of defect rate, optimization of die replacement time and reduction of die cost
Case Study #2
Identified defective products with scraps in between! Eliminated all inspections
Problem
- Rarely, small scraps are caught in the plate drawing process.
- To prevent defective products from leaking out, all products are inspected, but labor costs are high.
Countermeasure
- Replaced two dies fixing bolts with PiezoBolt to monitor load fluctuations
Result
- It was found that there was a difference (eccentricity) in the load applied to the left and right bolts when the scrap was sandwiched.
- Established a mechanism to detect waveforms that deviate from the moving average and send out an alarm.
Even small abnormalities are reliably caught and defective products are identified! We were able to eliminate all inspections.
Case Study #3
Punch breakage detection and equipment maintenance! Reduced costs by 2 million JPY per month!
Problem
- Large numbers of defective products were produced due to unnoticed punch breakage in press punching and forming.
- Punch debris causes damage to the die.
Countermeasure
- Replaced bolts fastening dies and plates with PiezoBolt to monitor load fluctuations
Result
- Minute changes in the forces applied to the product were found.
- By establishing a system to stop equipment when an abnormality is detected, the company succeeded in minimizing the number of defective products. Punch fragments are no longer being punched in.