Detecting tool crack propagation
Issue
Die cracking occurs in the forging process of automotive parts
- The die is not noticed until it cracks, and the cracks in the die forming area are transferred to the product, resulting in defective products.
- Visual inspections are conducted to prevent defective products from leaking out, but there is variation among operators.
- Periodic replacement of dies at short life settings is costly.
Solution
A ring-shaped jig is placed on the outer diameter of the die, and the ring is tightened with the piezoelectric load sensor "PiezoBolt".
We measured the cycle from the time the die was installed until it was damaged.
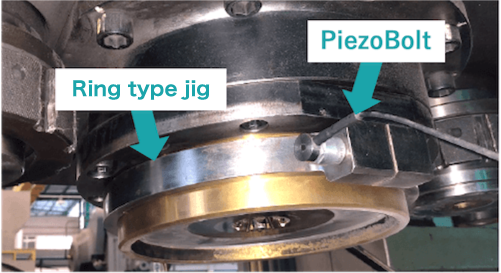
As a result, it was found that it is possible to detect minute vibrations when die cracks occur and pattern the degree of progress until they are transferred to the product by the number of abnormal waveforms that occur. By counting the number of abnormal waveforms that occur during production and establishing a system that sends out an alarm and stops the equipment when the number exceeds a set number, it is possible to prevent the outflow of defective products.
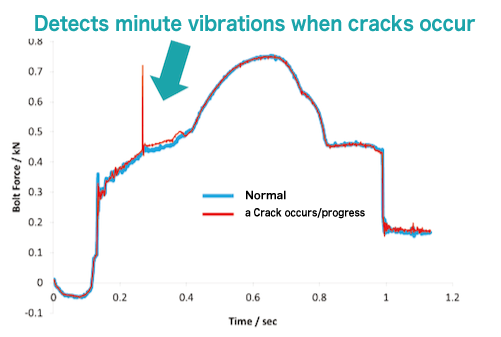
Result
Improved production efficiency through advance detection of die cracks
- The company was able to notice minute damage occurring inside the die, preventing mass production of defective products.
- Predicting the approaching life of the dies and regrinding the dies allows them to be used longer.
- Since production is now controlled by quantifying data rather than relying on individual workers, standardization of the production site has been achieved.
Customer Testimonials
The die itself did not require any modifications, the ring-type jig was easy to remove, and the load sensor was easy to install.
We plan to increase the number of applications, such as punch breakage, since it seems to be able to be rolled out beyond the die cracking.
Industry: Automobile parts manufacturer
Products Used:
- Piezoelectric load sensor PiezoBolt
- DeveloperSenses
- Wire type linear sensor
Case Study List
- Detecting tool crack propagation
- Die breakage detection
- Life prediction by punch abrasion
- Lubricant Evaluation
- Detecting punch breakage
- Foreign object strike detection
- Detecting adhesion of scrap
- Visualization of press forming
- Equipment maintenance of presses
- Failure detection of cutting tools
- Detecting anomaly of die casting