Lubricant Evaluation
Issue
Lack of quantitative means to evaluate lubricant performance
- Failure to identify performance differences due to application volume leads to high volume production of defective products.
- Differences in results between pre-evaluations and actual post-evaluations have led to on-site problems.
Solution
The piezoelectric load sensor "PiezoBolt" was installed at the point linked to the knockout load of the die measurement.
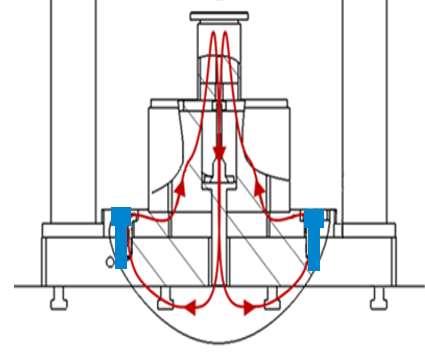
As a result, we detected differences in frictional resistance depending on the type and amount of lubricant applied. We also found that the load was completely different. By selecting the optimal type of lubricant and application conditions, we were able to make proposals to reduce the risk of damage due to the increased frictional resistance of the dies. In addition, the performance of the lubricant, which could not be determined from the list of ingredients alone, was clarified, leading to improved product reliability.
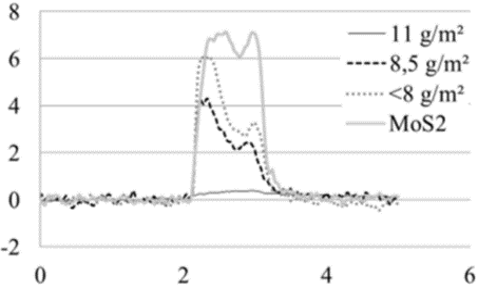
Result
Realize performance evaluation of lubricants to improve quality
- It was confirmed that changing the type and amount of lubricant produced completely different results even when the forming conditions were exactly the same.
- Reduced number and cost of prototype tests conducted to select optimum coating conditions.
- The lubrication condition can now be detected in real time by looking at the difference in the knockout load of the product, and the occurrence of die seizure and damage detection can also be performed.
Customer Testimonials
In addition to enabling quantitative evaluation of lubrication performance, which until now could not be managed numerically, the repeatability is good and the measurement results are easier to manage. We were attracted by the fact that the system can be used to measure any equipment as long as the bolt size is the same.
Industry: Lubricant manufacturer
Products Used:
- Piezoelectric Load Sensors PiezoBolt
- DeveloperSenses
- Wire type linear sensor
Case Study List
- Detecting tool crack propagation
- Die breakage detection
- Life prediction by punch abrasion
- Lubricant Evaluation
- Detecting punch breakage
- Foreign object strike detection
- Detecting adhesion of scrap
- Visualization of press forming
- Equipment maintenance of presses
- Failure detection of cutting tools
- Detecting anomaly of die casting