金型の破損には、成形中に金型を構成する材料が分断されてしまう「割れ」や、金型との接触部分の圧力が高くなり、異常摩擦が発生する「かじり」、生産を繰り返すうちに徐々に擦れ形状が変化してしまう「摩耗」などがあります。本記事では、金型の破損の種類から、発生原因や対策をご紹介します。
金型の破損の種類と原因
金型の破損とは、金型が成形中の何らかの原因で元の形状でなくなることを指します。
種類としては、割れ、かじり、摩耗、クラック、チッピング、変形などが挙げられます。
- 割れ金型を構成する材料の一部または全部が分断された状態
- かじり金型表面の一部が磨耗・脱落している状態
- 摩耗金型が徐々に擦れ形状が変化した状態
- クラック異常層が起点となり、金型に亀裂が生じた状態
- チッピング金型が部分的に欠損している状態
金型の破損が発生してしまう原因と、対策や事例について以下で詳しく説明します。
「割れ」の原因と対策
割れとは、金型を構成する材料の一部または全部が分断された状態のことです。
対策として、成形による発生応力の低減、靭性値の高い材質への変更、型構造の見直し(締め代変更)、表面処理方法の変更等により改善が期待できます。
当社では、破損した金型現品の調査(マイクロスコープ・切断調査)にて発生原因を特定し、CAE活用による型構造の見直し(STERECONの採用も含む)、レイアウト(工程形状)の変更を提案しています。
また、圧電式荷重センサー「PiezoBolt」を用いて、成形圧力の変動をモニタリングし、型割れ発生時に異常な振幅が生じることを検出することで不良品の大量流出防止を実現した事例もあります。
さらに詳しい情報を知りたい方は、以下リンクよりご覧ください。
「かじり」の原因と対策
かじりとは、金型と金型の間、または金型と材料間の摺動面に、凝着(焼き付き)の発生や高硬度片が入り込み、金型表面の一部が(多くはスジ状に)磨耗・脱落することです。
対策として、表面処理(コーティング・窒化など)追加、金型表面の粗さ改善、金型の硬度アップ、金型間のクリアランス見直し、被加工材の潤滑処理適正化等により改善が期待できます。
当社では、割れ対策同様に現品を確認し、コーティング変更、型表面の仕上げ変更、潤滑処理など生産条件の改善を提案しています。
また、圧電式荷重センサー「PiezoBolt」を用いて、かじりの一因である潤滑処理条件によるノックアウト荷重の違いを計測することにより、最適な潤滑剤・塗布条件の最適化を実現した事例もあります。
さらに詳しい情報を知りたい方は、以下リンクよりご覧ください。
「摩耗」の原因と対策
摩耗とは、成形時の金型と素材との摩擦により、金型が徐々に擦れ形状が変化した状態です。
対策として、成形時の潤滑剤の見直しや金型の面粗度の見直し、材質・表面処理の変更で改善が期待できます。
当社では、新品と摩耗による使用限界前のピーク荷重の差異を圧電式荷重センサー「PiezoBolt」で計測し、不良品を生じさせないよう監視した事例があります。
さらに詳しい情報を知りたい方は、以下リンクよりご覧ください。
工具の摩耗とは?荷重センサーを活用して摩耗の進行を見える化した事例を解説
「クラック」の原因と対策
クラックとは、金型最表面の急激な温度変化による非晶質層や放電加工による変質層などの異常層が起点となり亀裂となることを指します。
対策として、表層の内部品質が安定するような金型の加工方法の見直し、靭性値の高い材質への変更、成形時の熱管理等により改善が期待できます。
さらに詳しい情報を知りたい方は、以下リンクよりご覧ください。
クラックとは?荷重センサーを活用して小さなクラック発生を検知した事例を解説
「チッピング」の原因と対策
チッピングとは、成形時において金型に瞬間的に耐力を超えた応力が生じ、部分的に欠損する事象です。
対策として、潤滑剤の均一化により金型との摩擦状態を安定させたり、微小な異物の打ち込みなどを回避することで改善が期待できます。
当社では、チッピング発生時の僅かな発生荷重の違いを圧電式荷重センサー「PiezoBolt」を用いて計測し、設備を停止させ不良品の大量発生を防いだ事例があります。
さらに詳しい情報を知りたい方は、以下リンクよりご覧ください。
最後に
いかがだったでしょうか。
当社では、CAE技術、荷重センサーを用いたセンシング技術などを活用して、金型の破損を防ぐサポートをさせていただきます。
金型の破損による不良品流出に困っている、金型の損傷を未然に防ぎたい、などお困りごとがありましたら、お気軽にお問合せください。
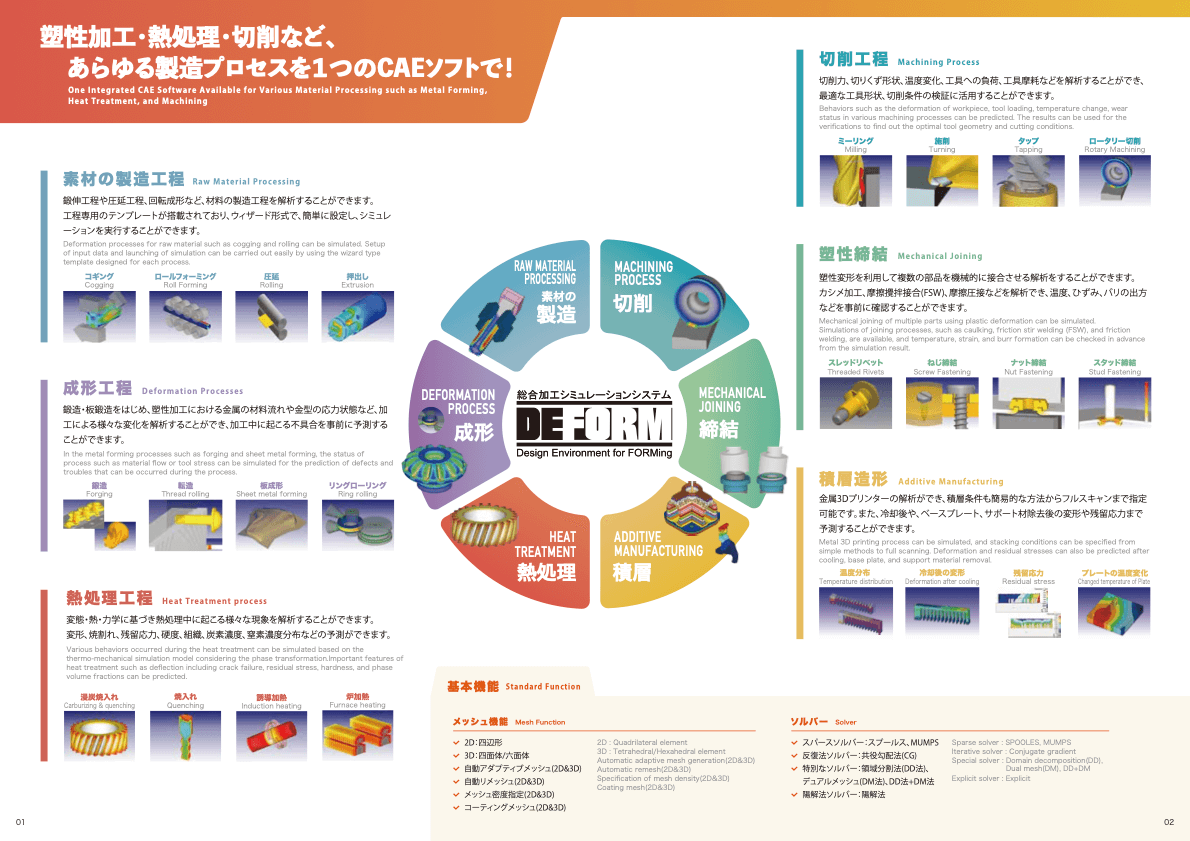
CAEソフト「DEFORM」カタログ
DEFORMは、鍛造・切削・かしめなど、あらゆる金属加工に対応した総合加工シミュレーションソフトです。対応できる工程、各種機能の詳細や事例をまとめた総合カタログです。
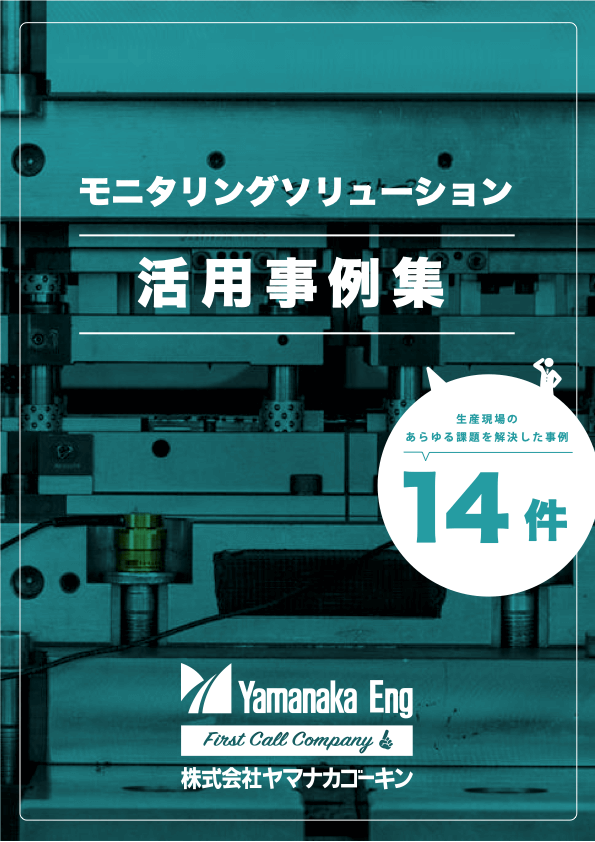