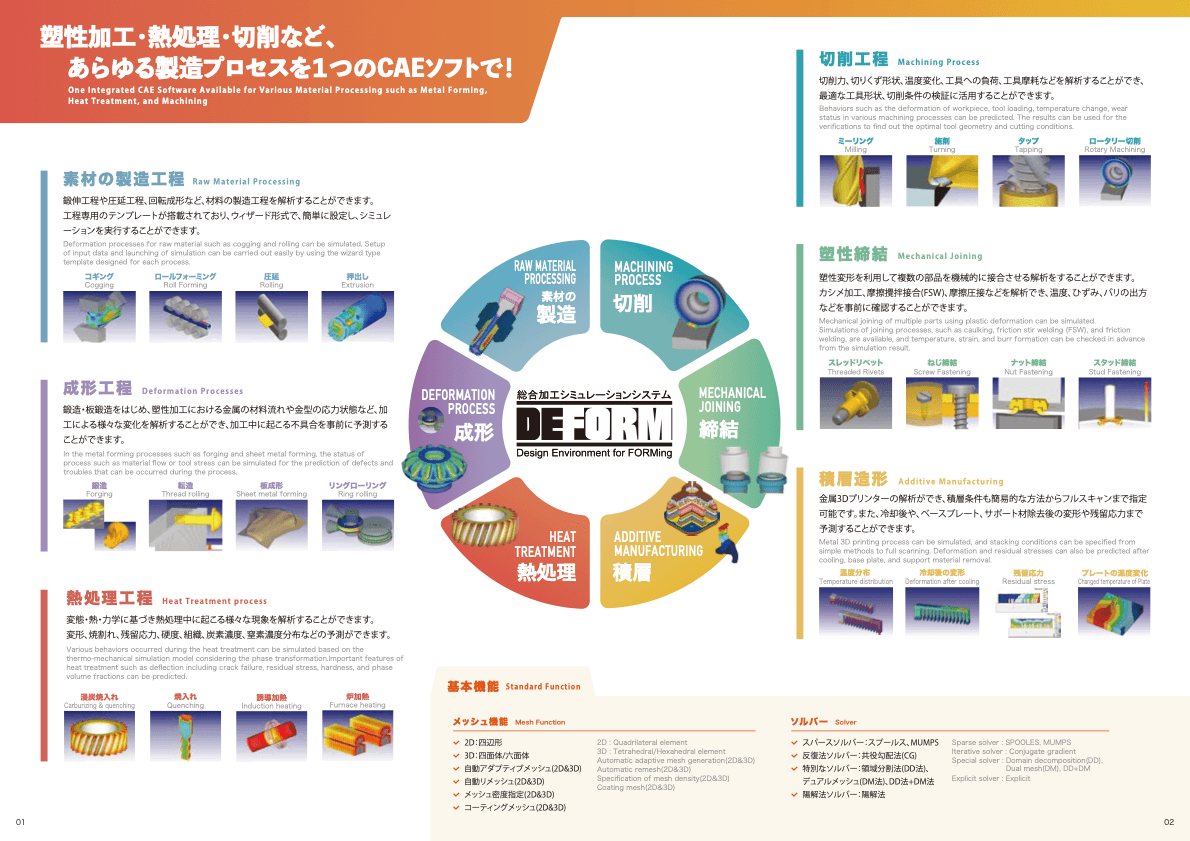
Release Date:2024/09/03
What are Metal Die Breakages? – Causes of Cracks, Galling, & Wear
Breakages of metal dies include:
- Fracture: Occurs when the die material separates into pieces during the forming process.
- Galling: Happens when the pressure (load) at the contact area between the die and the workpiece increases, causing abnormal friction.
- Wear: Gradual shape changes in the die caused by repeated friction during production.
In this article, we will introduce the types of metal die breakages, their causes, and their solutions.
Contents
Types of Metal Die Breakages and Causes
Breakages of metal dies occur during forming processes for various reasons, changing their designed shapes. Common types include:
- Fracture: The state where part or all of the die material separates into pieces.
- Galling: The state where part of the die surface is worn out or detaches due to abnormal friction.
- Wear: The state where the shape of the die gradually changes due to repeated friction.
- Crack: Cracks originating from abnormal layers or stress concentrations on the die.
- Chipping: Partial loss or breakage of the die material, resulting in missing sections.
We will explain the causes of each breakage, the solution, and the case study below.
Causes of Fracture and Solutions
Fracture refers to the state where part of or all of the die material separates into pieces.
Solutions:
- Reducing stress generated during forming.
- Changing the material to one with higher toughness.
- Reviewing and modifying the die structure (e.g., interface adjustments).
- Changing the surface treatment method.
We offer solutions such as:
- Identifying the causes of fractures by inspecting actual dis using microscopes or cutting analysis.
- Reviewing and modifying the die structure with CAE (including utilizing containers by STRECON).
- Changing the layout (process and shape)
Additionally, we have experience in preventing the mass production of defective products by using our piezoelectric load sensor “PiezoBolt”, to monitor forming pressure changes and defect abnormal amplitude when fractures occur.
For more detailed information, please click the link below.
WHAT IS A FRACTURE? – CAUSES AND SOLUTIONS
Causes of Galling and Solutions
Galling refers to the state where part of the die surface is worn out or detached (often in streaks) due to seizures or the intrusion of hard particles between the die components or between the die and the material.
Solutions:
- Adding surface treatment (eg., coating, nitriding).
- Improving the roughness of the die surface.
- Increasing the hardness of the die.
- Reviewing and modifying the clearance between die components.
- Optimizing the lubrication treatment of the workpiece.
We offer solutions such as:
- Inspecting actual dies and proposing changes to coating treatment.
- Modifying the finishing process of the die surface.
- Improving production conditions, including lubrication treatment.
Additionally, we have experience in optimizing lubricant conditions by measuring how knockout load changes in optimizing lubricant conditions by measuring how knockout load changes based on lubrication treatment conditions using our piezoelectric load sensor, PiezoBolt.
For more detailed information, please click the link below.
WHAT IS GALLING? – CAUSES, PREVENTION STRATEGIES, AND CASE STUDY
Causes of Wear and Solutions
Wear refers to the state where the shape of the die gradually changes due to friction between the die and the material during the forming process.
Solutions:
- Reviewing and changing the lubricants.
- Modifying the asperities (surface roughness) on the die surface.
- Changing the material and surface treatments.
We also have experience in monitoring and preventing defective products by measuring the difference in peak load between new and worn-out dies before reaching their usage limit. This is achieved using our piezoelectric load sensor “PiezoBolt”.
For more detailed information, please click the link below.
WHAT IS WEAR? VISUALIZE WEAR PROGRESSION WITH YAMANAKA ENG’S LOAD SENSOR
Causes of Cracks and Solutions
Crack refers to the state where cracks originate from abnormal layers, such as amorphous layers caused by rapid temperature changes on the topmost surface of the die, or affected layers caused by electrical discharge machining.
Solutions:
- Reviewing and changing the die processing methods to stabilize the internal quality of the surface layer.
- Switching and changing the die processing methods to stabilize the internal quality of the surface layer.
- Managing heat during the forming processes.
For more detailed information, please click the link below.
WHAT ARE CRACKS? DIE CRACK DETECTION WITH YAMANAKA ENG’S LOAD SENSOR
Causes of Chipping and Solutions
Chipping refers to the state where part of the die is missing because the stress temporarily exceeded the proof stress during the forming process.
Solutions:
- Stabilizing the friction state of the die by ensuring uniform application of lubricants.
- Preventing the intrusion of tiny foreign objects during the forming process.
We also have experience in preventing the mass production of defective products by using our piezoelectric load sensor “PiezoBolt” to measure slight differences in load when chipping occurs. This allows the equipment to stop immediately, preventing further damage.
For more detailed information, please click the link below.
WHAT IS CHIPPING? – CAUSES AND SOLUTIONS WITH YAMANAKA ENG’S LOAD SENSOR
How Can We Help?
We hope you found this article helpful.
At our company, we provide support to prevent metal die breakages by utilizing CAE technology and sensing technology with load sensors. If you are facing issues such as defective products caused by die breakages or are looking for ways to prevent die damage in advance, please feel free to contact us. We are here to assist you.