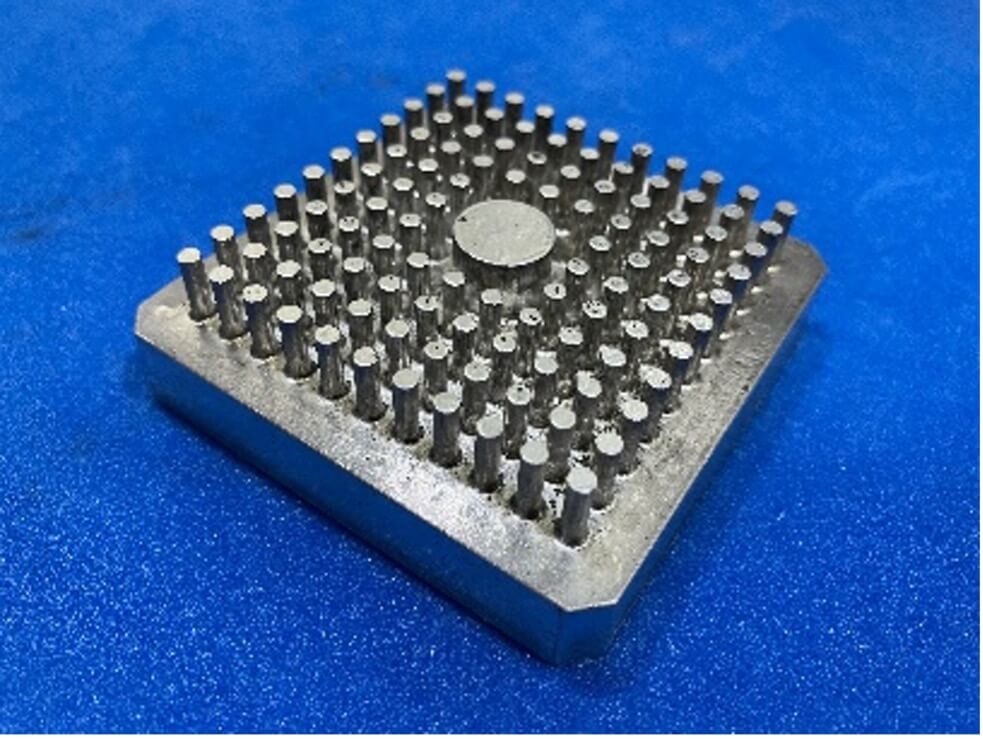
Release Date:2024/09/02
What is the Optimal Solution for Manufacturing Heat Sinks? – Benefits of Forging & Key Points
What is a Heat Sink?
A Heat Sink is a component that absorbs heat and dissipates it into the air. It is also known as “radiator” and “radiating sheet/plate”. Materials with high thermal conductivity, such as nonferrous metals like aluminum and copper, are used for heat sinks.
Semiconductors are used in various fields, including electronic devices and automotive components. However, many semiconductors generate heat when electricity flows, and if they remain at high temperatures, it can lead to malfunctions or failures. To prevent these issues, heat sinks are employed to dissipate heat effectively.
Structure of a Heat Sink
The efficiency of heat dissipation improves with a larger surface area in contact with the air.
Therefore, heat sinks are designed with multiple thin plates or rods, known as “fins”.
The performance of a heat sink is measured by its thermal resistance (℃/W or K/W). This metric indicates how difficult it is for heat to conduct through the material; a lower value signifies better performance.
Design of Heat Sink
Heat Sinks are primarily manufactured using die-casting, machining, and extrusion methods; however, these methods face challenges related to quality, cost, and geometric limitations.
As an alternative, forging has gained attention recently because it can address these issues in a well-balanced manner. Consequently, the demand for heat sinks used in automotive inverters has been increasing and is expected to accelerate further. Additionally, the push for carbon neutrality, which emphasizes material reduction, and the need for improved material yield due to rising raw material costs are also contributing factors to the growing demand for forging.
Forging Heat Sink
What are the benefits of manufacturing heat sinks using the forging method?
First, forging is similar to extrusion but utilizes back pressure to form fins, resulting in uniform length. This eliminates the need for cutting processes required in extrusion, allowing the product to be used directly. As a result, yield improves, and costs are reduced. Furthermore, forging enables continuous processing with a press machine, leading to high productivity.
Additionally, by incorporating fin shapes into the die design, it is possible to create not only simple round and square shapes but also more complex designs that enhance thermal dissipation. This expands the specifications and capabilities of heat sinks.
Now, we will highlight key points for heat sinks through forging, using our prototype heat sink as an example.
Prototype
We created prototypes of the heat sink using both aluminum and copper.
Both materials were processed at a temperature between 350 to 400℃, while the metal dies were maintained at 200℃ during forming. The forming loads and back pressures were as follows:
- Aluminum: Forming Load 430t (Surface Pressure 105kg/mm2), Back Pressure 10t
- Copper: Forming Load 540t (Surface Pressure 130kg/mm2), Back Pressure 10t
Key Point of Heat Sink Design
One of the key points in heat sink is to apply back pressure to the geometry. This means exerting constant pressure on the die that contacts the workpiece, which helps push the material back. By doing so, you can achieve consistent fin heights with minimal variation.
In this project, we utilized CAE analysis, which allowed us to assess the stress on the dies, identify underfills, and detect scratches on the material during forming. This enabled us to evaluate optimal shapes and materials before prototyping.
As a result, this simulation helped us reduce the number of prototypes needed. Additionally, we were able to lower development costs and labor, as well as shorten the overall development time.
Conclusion
Thank you for reading! We hope you found this article informative.
In this article, we discussed the overview of heat sinks, the benefits of forging, and key design points. Yamanaka Eng is equipped with the necessary facilities and equipment for prototyping, including a multi-axis servo press, heating furnace, temperature regulators for dies, and release agent application devices.
By effectively utilizing forming simulations, we can help reduce costs and manufacturing processes. If you are interested in designing new products or would like more information, please feel free to contact us.