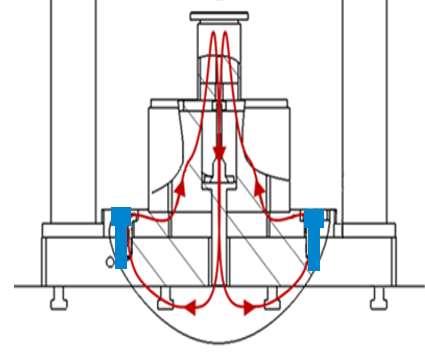
Release Date:2024/09/03
What is Galling? – Causes, Prevention Strategies, & Case Study
What is Galling?
Galling in metal forming refers to the phenomenon where carbides in the workpiece become high-hardness pieces that scrape off parts of the die surface. It also refers to the falling off of the die material due to sliding between the upper die and lower die, or between the die and the workpiece.
Causes of Galling on Metal Dies
Galling occurs through the forming processes. The main reasons for galling are: Adhesion between the workpiece and the uneven die surfaces, temperature rise caused by forming and sliding, and wear of the die surface.
Types of Galling
Galling in metal dies can be classified by its causes:
- Abrasive wear:
This refers to the phenomenon where a soft material is scraped by a hard material, and a hard foreign substance between the sliding metals scrapes their surfaces. This phenomenon is more likely to occur when there is a significant difference in hardness between the dies and the materials.
- Seizure:
Seizure occurs where fine asperities on the sliding surfaces collide, causing them to adhere due to the heat generated. The adhered parts then detach and wear away, which is also referred to as “galling.”
- Fatigue wear:
Fatigue wear occurs when metal dies repeatedly move and stop, leading to metal fatigue and subsequent wear.
- Fretting wear:
Fretting wear occurs when two contacting solid surfaces rub against each other with very small amplitudes. This contact generates significant heat, and the presence of red rust is a characteristic feature of this type of wear.
- Corrosion wear:
Corrosion wear occurs when the die is corroded due to the deterioration of lubricants.
How to Prevent Galling
Continuing production with galling present on the die can lead to defective products. To prevent galling, the following measures are recommended:
- Implementing surface treatments (such as coating and nitriding).
- Modifying the surface roughness of the die.
- Increasing the hardness of the die.
- Reviewing and adjusting the clearance between the die and the workpiece.
- Optimizing the lubrication treatment process for the workpiece.
However, optimizing the lubrication treatment process is not straightforward, as it can be significantly affected by the type of lubricant used and the amount applied.
In the following section, we will introduce a case study focused on lubricant monitoring, which enables real-time detection of galling (seizure) conditions.
Case Study: Evaluate Lubricant Performance and Select Optimal Application Conditions
In this case study, the customer encountered the following challenges during the foreign process:
- Inability to assess the differences in effectiveness based on the amount of lubricant applied, resulting in the production of a large number of defective products.
- Discrepancies between the friction performance results from preliminary evaluations and actual performance in the field, leading to operational issues.
Solution
As a measure, we installed two Bolt Piezoelectric Load Sensors called “PiezoBolt” at the location corresponding to the knockout load of the die and conducted measurements.
※What is the Bolt Piezoelectric Load Sensor “PiezoBolt”?
PiezoBolt is the load sensor with an embedded sensor unit using a piezoelectric element inside the bolt. It is capable of measuring minute load changes by leveraging the piezoelectric effect, which generates voltage when force (pressure) is applied.
For more detailed information, please click the link below.
Result
As a result, we discovered that the measurement results varied when the type and amount of lubricant applied were different, even though the forming conditions remained the same. This finding suggests that the costs and number of trial tests required to select the optimal application conditions can be reduced. Additionally, by monitoring the differences in the knockout load, we can now detect lubricant conditions in real-time, as well as identify occurrences of seizure and breakage in the die.
Conclusion
Thank you for reading.
There are various ways to prevent galling, and this time we focused on a solution with our load sensor.
If you think of introducing this solution in your production site, or have troubles with defects other than wear, such as cracks and galling, please contact us.