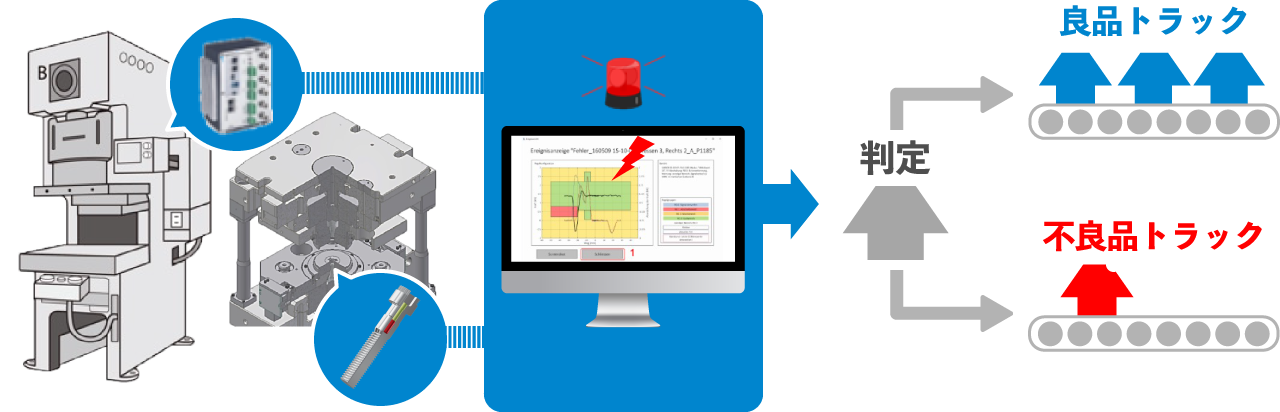
Release Date:2024/09/03
Say Goodbye to Full Inspection with Yamanaka Eng’s Smart Forging System for Defect Detection
Do you find yourself thinking:
“Full inspection costs a lot. How can we reduce time and save money?”
“No more defective products should leave the factory.”
Our Smart Forging System can determine whether the products are good or defective at the moment they are forged and sort them accordingly.
In this article, we will introduce the basics of full inspection, an overview of die sets, and our Smart Forging System, along with a case study.
If you are considering abolishing full inspections and preventing defective products without replacing your press machines, this article is for you.
Contents
1 Minute Introduction – the Smart Forging System
What is Full Inspection/100% Inspection?
Full inspection refers to the process of inspecting all products individually.
This method is highly affective for guaranteeing product quality, as it can exclude defective products and ensure only good products are selected.
There are various ways to conducts full inspections, with the most common being:
- Visual Inspection by People
- Mechanical Inspection Using AI and IoT Technology
Visual Inspection by People
Visual inspection is a straightforward and accesible method, especially if you have enough personnel. However, it comes with significant drawbacks:
- High Accuracy: Machines are far less likely to miss defects and can accurately distinguish between good and defective products.
- Speed and Efficiency: Inspections are completed quickly, improving overall efficiency.
- Reduced Labor Costs: Automated inspections eliminate the need for human involvement, significantly reducing labor costs.
What is a Die Set?
A Die Set is a set of accessories used to fix metal dies onto a press machine during press working processes.
A die set comprises several components, including
- Upper and lower dies
- Spacers
- Holders
- Guide posts
- Die plates
To produce high-precision products, it is crucial to maintain the concentricity of the upper and lower dies accuracy. Additionally, the ease of replacing dies and other components, as well as their maintainability, are essential factors for improving precision and accuracy.
For more detailed information, please click the link below.
DIE SETS OFFERED BY YAMANAKA ENG
What is the Smart Forging System?
The Smart Forging System is a system developed by us to prevent defective products from leaving the factory.
By using sensors mounted on the die set, the system visualizes the state of the die and the process. It detects changes in the state of state of defective products compared to good products, allowing defective products to be sorted out automatically. Since the system can distinguish between good and defective products without human intervention, there is no need for full inspection.
This system is applicable to all types of component production using press working methods. It is suitable for both masss production and the production of high-precision components, such as automotive parts.
Key Features:
Die Load Visualization and Management
- The system visualizes and quantifies the load state of the dies, enabling effective die life management.
Equipment Abnormality Detection
- In addition tot detecting abnormalities in dies, the system can also identify issues in die sets and press machine, making it a valuable tool for equipment maintenance.
Components of Smart Forging System
The Smart Forging System developed by us is consists of a die set and the following components:
- Piezoelectric Load Sensor “PiezoBolt”: Measures the load applied to the dies and die sets.
- Dedicated Monitoring System “EdgeSenses”: Analyzes data received from PiezoBolt.
- Rotary Beacon Light: Alerts operators when defective products are detected.
- Chute: Sorts out defective products automatically.
Case Study
Here, we introduce a case study where the Smart Forging System was used to monitor the load state of forging dies and die sets during the forging process, enabling the detection of defective products and preventing their release from the factory.
In this case:
- PiezoBolt was mounted on a ring-shaped jig attached to the outside of the die.
- The system visualized the elastic-plastic behavior of the die, which synchronized with the filling conditions of the products, allowing the detection of unfilled defective products.
- Monitoring rules were set in the system to compare the process of unfilled defective products with that of good products.
- When unfilled defective products were detected, the rotary beacon light altered operators, and the chute automatically sorted out the defective products, preventing their release.
Conclusion
Thank you for reading! We hope you found this article helpful.
With our Smart Forging System, you can automatically extract only good products, eliminating the need for full inspection. This reduces labor costs and improves product quality by eliminating the risk of human error.
In addition to the Smart Forging System, we offer other products and services, such as the Self-Aligning Die Set and the High-Precision Forging System, to help solve challenges at your production sites.
If you would like to learn more or explore how these solutions can be applied to your operations, please feel free to contact us.