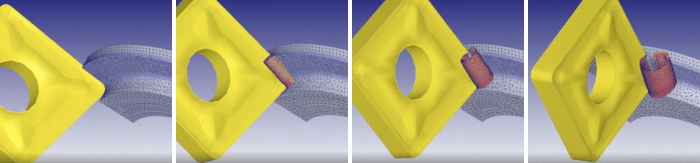
Release Date:2024/09/03
What is Machining/Cutting Simulation with CAE? – Benefits & Case Studies
By utilizing CAE (Computer-Aided Engineering) in metal machining/cutting, you can predict chip shapes and cutting forces during the process. This enables you to optimize tool shapes and cutting conditions, ultimately improving the lifespan of cutting tools.
In this article, we will provide an overview of Machining/Cutting, discuss the benefits of CAE analysis, and share case studies.
Contents
What is Machining/Cutting?
Machining, also known as cutting, is a method of forming metals into desired shapes by removing the unnecessary parts of the metal as chips using a cutting tool. The cutting tool must be harder than the workpiece.
Advantages:
- Enables the creation of shapes that are difficult or impossible to achieve with other material forming methods.
- Precision and quality have improved significantly due to advancements in machinery and tools.
- Does not require dies, making it suitable for small production runs and short delivery times.
Disadvantages:
- Produces chips that become scrap, impacting costs.
- Has lower productivity compared to plastic forming processes like pressing.
Types of Machining/Cutting:
Rotary Machining/Cutting:
- Includes turning and boring with a cutting tool, drilling, tapping, gear hobbing, milling, and grinding with a grinding wheel.
Linear Machining/Cutting:
- Includes broaching and gear shaping.
Benefits of CAE Analysis for Machining/Cutting
CAE analysis for machining/cutting enables you to predict the shapes and cutting forces during the process. This allows you to optimize tool shapes and cutting conditions, extending tool life and reducing machining costs.
Additionally, CAE analysis can predict shape changes after machining, considering residual stress from prior forming processes. By optimizing machining paths, you can avoid deformation in subsequent processes, further reducing production costs.
Examples of Cutting/Machining Simulations with CAE Solution
Now, we will introduce you examples of simulations using the CAE software DEFORM.
※What is the CAE software “DEFORM”?
DEFORM is a comprehensive machining simulation software for all types of metal processes, including forging, cutting, and heat treatment.
With a wide variety of analysis functions, our customers come from all fields, including the automotive, steel, aerospace, electrical/electronics, and chemical industries.
For more detailed information, please click the link below.
The CAE software “DEFORM” is your best partner in plastic forming
Other Case Studies (Click on the image to visit the 3D animation page)
These are case studies of turning, milling, and deformation predictions after machining/cutting.
Chip shapes vary depending on the machining method, conditions, and material properties. Residual stress from prior processes can also influence the deformation of the material after machining.
Conclusion
Thank you for reading. We hope you enjoyed this article.
By utilizing CAE, it is possible to prevent defects in advance, while also reducing costs and shortening lead times. The CAE software DEFORM offers a wide range of features to support designers, including capabilities for additional processes, data analysis, experimental design modules, and optimization modules.
If you have any questions or concerns regarding product design or manufacturing, please feel free to contact us.