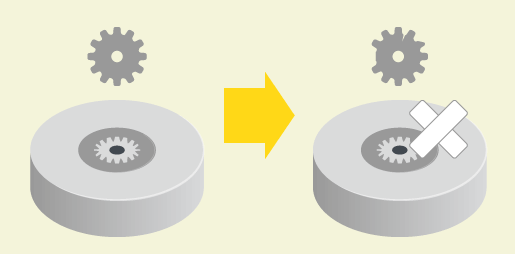
Release Date:2024/09/03
What is Die Life? – Shot Counts & Materials Determine Die Life in Cold Forging
Contents
What is Die Life?
Die life is the length of how long the die can be used for forming metals.
Forming metals under certain conditions can cause issues such as wearing, galling, peeling of the surface of the die, and cracks on it, making it impossible to guarantee product quality and production. Dies in those conditions have been reached to the end of their life.
Differences Between Die Life and Service Life
The term “service life” of a die is used to calculate depreciation for accounting purposes. In production environments, the standard life of a cold forging die is generally set at 10000 shots or more. However, due to the high productivity of cold forging, it is not uncommon for a new die to be replaced within just a few days.
For this reason, cold forging dies are often treated as operating costs (production expenses), which differs from the costs (investment depreciation) associated with dies that have a longer service life, such as aluminum die casting dies and body press dies. Despite all being part of the plastic forming processes, the handling and accounting for these dies can vary significantly,
Factors That Determine Die Life
There are various types of dies, each with its own characteristics, and all have a defined die life. The die life is influenced by usage conditions and materials. The primary factors that determine die life include shot count and die materials.
Shot Count
Shout count refers to the number of times a die is used for forming. Before manufacturing the die, calculations are performed to estimate how many shots it can withstand.
Materials for Die
The durability of a die varies depending on the materials used.
For dies that are expected to endure a high number of shots, steel (either melted or powdered) or cemented carbide is commonly used. It is crucial to select the appropriate material based on its intended purpose, such as choosing materials with high wear resistance or those that are tough and resistant to cracking.
How to Extend Die Life
Die life varies depending on the number of shots.
〜1,000 Shots
When a newly manufactured die breaks after approximately 1,000 shots from the beginning of the process, the forming pressure likely exceeds the intended strength of the materials or the die design. In this case, it is essential to reevaluate the process design, die materials, structure, and dimensions, focusing primarily on geometric data.
1,000 Shots 〜10,000 Shots
When a die breaks after approximately 1,000-10,000 shots, it is most likely due to abnormal machining layers that arise during the manufacturing process of the die surface. These defects can result from various factors, including machining, electrical discharge machining, heat treatment, pre-treatment of the surface, and the condition of the final finished surface. In this case, it is essential to review and improve the management conditions of the die manufacturing process based on historical records.
10,000 Shots〜
When a die breaks after approximately 10,000 shots, it likely meets the die life requirements for each manufacturing process. To further enhance die life, it is important to consider measures such as improving the toughness or hardness of the materials, as well as reviewing the specifications to align with the forming process. Additionally, implementing new surface treatments or reassessing the types of treatments used can yield unique benefits.
Conclusion
Thank you for reading.
At Yamanaka Engineering, we have manufactured a wide range of precision forging dies based on the forging technology we have developed over the years. Our cold forging dies, in particular, are known for their high precision and strength. As pioneers in carbide die manufacturing, we take pride in delivering industry-leading accuracy and quality in our cold forging dies.
If you have any questions about selecting the appropriate die material, extending die life, or designing and manufacturing such parts, please feel free to contact us.