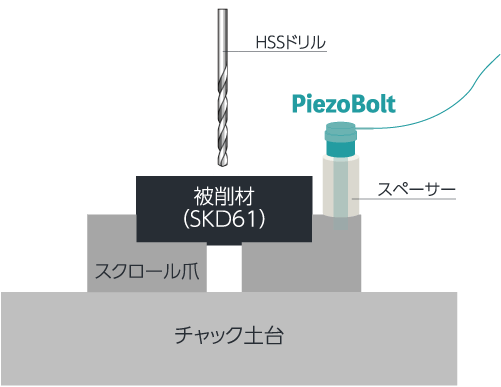
Release Date:2025/04/22
What is Wear? Visualize Wear Progression with Yamanaka Eng’s Load Sensor
What is Wear?
Wear refers to the gradual change and deterioration of the surface of a die or tool caused by friction with the material during forming.
Continuing to use worn tools without replacement can lead not only to a decline in machining accuracy but also to a reduction in production speed. Therefore, regularly checking the conditions of dies and tools is crucial for maintaining efficient production.
In this article, we will focus on discussing Tool Wear in cutting processes.
Types of Tool Wear
There are two well-known types of tool wear:
- Flank Wear:
Flank wear occurs on the clearance face (underside of the tool) when the workpiece abrades the tool, resulting in linear-shaped scars on the tool surface.
Note: The surface that scoops chips from the workpiece is called the rake face, while the surface perpendicular to the rake face is referred to as the clearance face.
- Crater Wear:
Crater wear occurs on the rake face of a cutting tool. It is characterized by a crater-like depression formed as chips from the workpiece abrade the cutting edge.
Measures for Tool Wear
Flank wear and crater wear occur on tool surfaces due to factors such as material, cutting speed, and feed rate of cutting tools. The following methods are effective in reducing wear:
- Reduce machining/cutting speed
- Increase feed rate
- Use tool materials with higher wear resistance
- Use coated tools
By optimizing cutting/machining conditions in this way, it is possible to slow down the progression of wear to some extent. However, it is impossible to completely prevent wear itself. As long as machining continues, wear will inevitably occur over time.
Regular replacement of tools, where limits are set for operation hours or usage cycles and tools are replaced before exceeding these limits, is a common practice.
While regular replacement is effective in preventing defective products, it is inefficient in terms of cost because tools are replaced before reaching their full lifespan. Additionally, it cannot address sudden tool damage that may lead to machining defects.
Ideally, cutting tools should be restored or replaced based on actual wear progression rather than estimated tool life. In the following section, we will introduce a case study where load sensors were utilized to detect tool wear progression during machining. We encourage you to read on for more details.
Case Study: Wear Detection of Cutting Tool, and Timing Optimization for Replacement
In this case study, the customer faced the following challenges during the machining process:
- Despite continuous monitoring by operators, a large number of defective products were produced.
- Tool replacement timing varied depending on the operator.
- Predicting abnormalities and identifying their occurrence using AE (Acoustic Emission). Sensors proved difficult.
Solution
As for the solution, we replaced the bolt that clamped the workpiece with Bolt Piezoelectric Load Sensor “PiezoBolt”, and measured the vibration behavior of the tool through a machining process.
※What is the Bolt Piezoelectric Load Sensor “PiezoBolt”?
“PiezoBolt” is a load sensor with an embedded sensor unit using a piezoelectric element inside the bolt. It is capable of measuring minute load changes by leveraging the piezoelectric effect, which generates voltage when force (pressure) is applied.
For more detailed information, please click the link below.
Result
As a result, we were able to detect changes for defective occurrences such as breakage, wear, and deformation of the cutting tool.
The data of defectives on the cutting tool and transmitting alert signals enables the automatic pause of the process right before a defect occurs. The solution enables replacing cutting tools at the best time, stopping the manufacturing process before wear grows.
Conclusion
Hopefully, this article fulfilled your curiosity and brought joy.
There are some ways to prevent wear of dies and toolings, and this time we have demonstrated a solution with our load sensor.
If you think of introducing this solution in your production site, or have troubles with defects other than wear, such as cracks and galling, please contact us.