IoTを活用したスマートファクトリー実現のための基盤技術として、あらゆるものにセンサーを組込み、取得した膨大な数値情報のビッグデータ解析やAI技術への期待が世界各国で一層の高まりを見せています。
当社でも、センシング技術と鍛造シミュレーションを活用することで製造工程の見える化や異常検知、設備保全などに適用可能な基盤技術の開発に取り組んでいます。
今回は、圧電式荷重センサーPiezoBoltおよび専用計測装置を切削加工(ドリル加工)に適用して「工具破損の予兆を検知した事例」をご紹介させていただきます。
目次
切削加工(ドリル加工)における工具破損の代表的な防止方法
切削加工において、工具破損を未然に防ぐ方法は主に以下の2つです。
作業員が工具交換タイミングを判断
作業員が切削中の音や振動、切粉の色、においの変化など感覚で判定を行うことで、工具の交換タイミングを判断します。ただ、この方法ですと、作業者によって工具交換タイミングにばらつきが生じてしまったり、作業者の退職や異動といったイベントによって工具交換のタイミングが見極められなくなったりする、といった課題があります。
工具寿命を設定
工具の実寿命より短く定めた寿命で管理・運用することで、工具が破損する前に工具交換できます。ただ、この方法ですと、工具本来の寿命ギリギリまで使用することができないため、工具コストがかかるといった課題があります。また、短く寿命を設定していたとしても設備や環境によって想定していた寿命よりも早く工具が破損する恐れもあり、確実な対策とはいえません。
したがって、工具破損を未然に防ぐには「人の技能に頼る部分を定量化・数値化する」「工具破損の予兆を正確に検知する」の2つが必要となります。
当社では、これをモニタリングソリューションというボルト型の荷重センサーを使用したサービスでサポートが可能です。ここからは実際の事例をご紹介します。
【事例】切削中の振動をセンシングして工具破損を防止
抱えていたお悩み
このお客様は以下のお悩みを抱えていました。
- 加工中は、作業者がほぼ付きっ切りで音を聞きながら監視を行っているが不良が多発する
- 監視する作業者によって、工具交換のタイミングが異なる
- AEセンサーを試してみたが、異常発生の予兆や発生時の特定が難しい
ボルト型荷重センサーPiezoBoltおよび専用計測システムの設置方法
左図は被削材を固定する治具の締結用ボルト(M12)をボルト型荷重センサーPiezoBoltに置き換え取付けた状態です。PiezoBoltはボルト内部にピエゾ素子を埋設した圧電式荷重センサーです。切削中の荷重変動や振動は固定治具を通じてPiezoBoltの締結部へ伝わり、電気信号として出力されます。電気信号の収集タイミングは用意した波形生成器により3秒間隔で2秒間の計測を行うトリガー信号を作成し、専用計測装置へ与えました。また、専用計測装置では2秒間をサンプリングレート10kHzで計測しています。
被削材には直径100mm、高さ50mmの円柱状SKD61を用い、直径10mmのHSSドリルで深さ22mmまで穴を形成するドリル加工を繰り返し行い、PiezoBoltの荷重変化と異常信号検知の有無を確認しました。
切削加工(ドリル加工)のセンシング結果
PiezoBoltで検出した振動幅(最大―最小)をプロットした分布図(横軸は時間、青点で表示)、単位時間(分)当たりのデータ数を示す棒グラフを以下に示します。
11回目に異音が発生し中止しましたが、それに至るまでの7回目と10回目、11回目の分布にばらつきが確認できます。振動幅が増加した7回目と10回目の異常時の波形を正常時の波形と重ね比較したグラフがその下図です。工具の摩耗や破損により被削材固定治具が受ける負荷荷重は増加することがわかります。
PiezoBoltで工具劣化時の加工力の変化や振動パターンの変化を検出できることが確認できました。
センシングすることにより、経験的なカンやノウハウの定量評価が可能になります。これにより、工具の適切な交換時期を把握でき、不要な不具合対応を回避。生産性の向上につなげられるでしょう。
最後に
いかがだったでしょうか。
本事例をさらに発展させると、基準信号と異常信号との差異から状態を判断、判定することにより、警報や非常停止・フィードバック制御などが可能です。今回は、切削加工(ドリル加工)の事例をご紹介しましたが、他にも鍛造、プレス加工、鋳造などにも適用した事例もあります。お困りになられていることがあれば、お気軽にお問合せください。
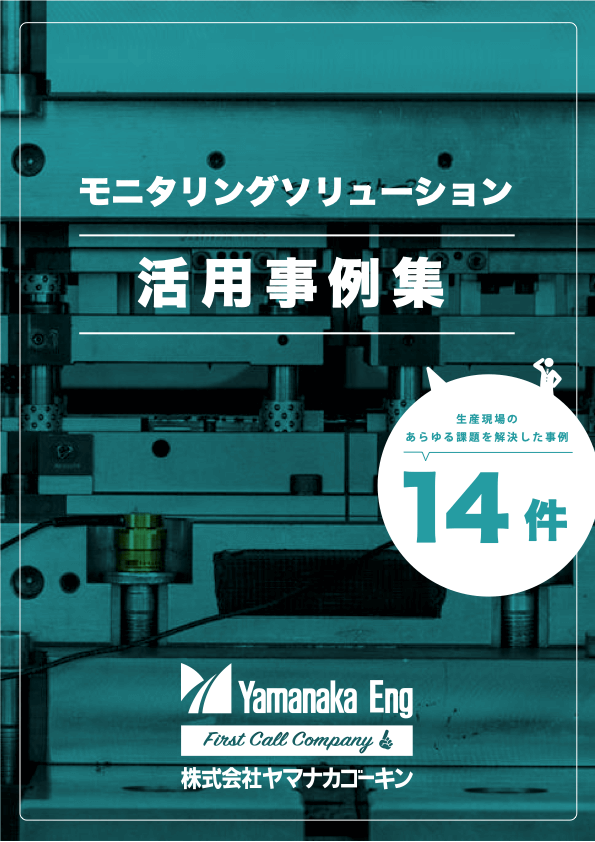